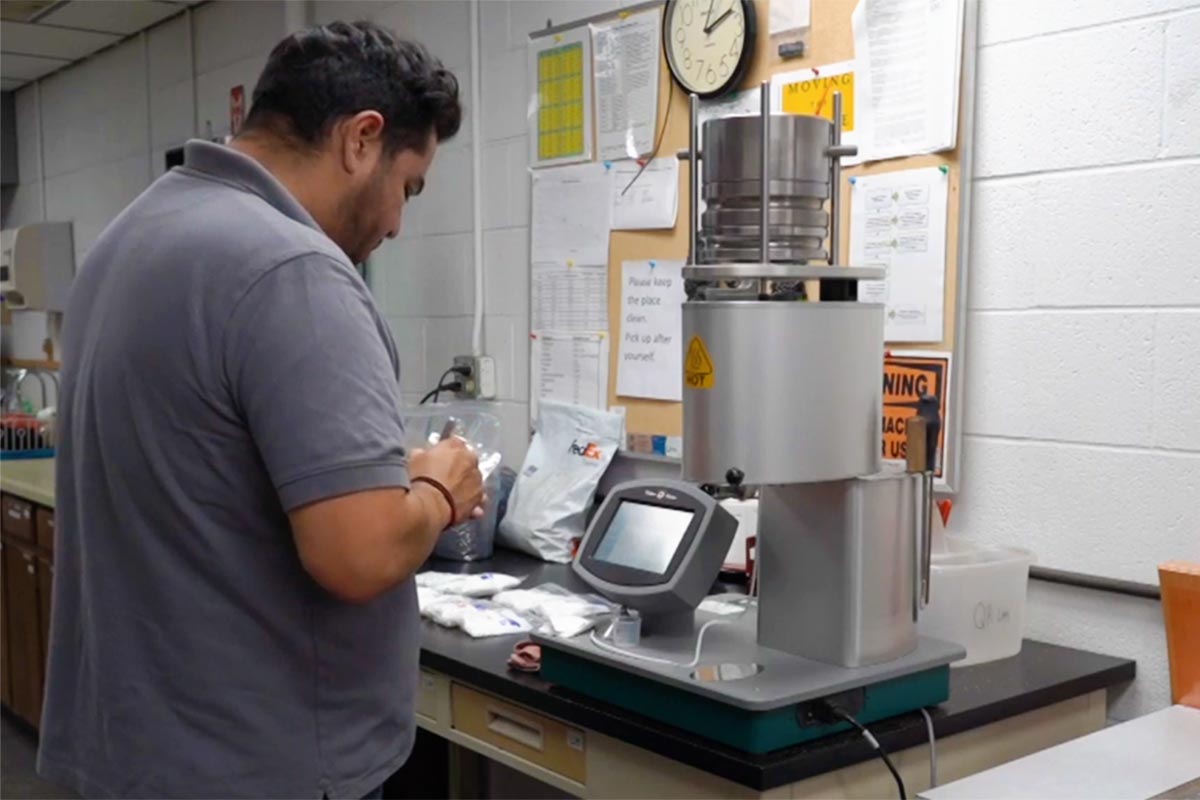
Learn about our quality testing process and our certifications as a large thermoforming manufacturer.
At Penda, we take pride in creating new products and solutions you may have never thought possible through our thermoforming capabilities. Since becoming a Tier 1 supplier and manufacturer for leading OEMs across the globe, we’ve placed a focus on our commitment to quality by refining processes and ensuring proper testing is done at our facilities.
In doing this, we’ve ensured the satisfaction of the consumers and businesses we’ve partnered with by guaranteeing that the solutions we create meet the highest standards. Our involved testing process is what truly sets us apart in the industry. First, we test our inbound materials each day to ensure they are quality components for use on our production floor. Then, once we create a thermoformed solution, it too undergoes rigorous testing to ensure that it meets the demands of your industry. This dedication to quality made us one of the first organizations to earn IATF 16949 certification. This isn’t the only certification that sets us apart though.
Our Certifications
Ford Q1 Certification
Achieving the Ford Q1 certification means that a supplier’s facility or manufacturing site has achieved excellence in five important areas: capable systems, continuous improvement, high performance, superior manufacturing process, and satisfied customers. The mark is considered worldwide as an indication of exceptional quality, which is exactly what our solutions are. Organizations achieving Ford Q1 Certification can guarantee 100% on-time delivery and service.
IATF 16949:2016
This standard focuses on the development of a quality management system that allows for continuous improvement, an emphasis on defect prevention, and the reduction of variation and waste in an organization’s supply chain. Penda’s facilities in Portage, Wisconsin, and Lerma, Mexico are certified to the IATF 16949:2016 standard. Organizations that meet this standard ensure their supply-chain process stands up to the rigorous standards of the Automotive industry, while we focus on maintaining this standard, we always focus on improving out supply chain above and beyond what is expected in the industry to the highest possible levels of service we can provide for our customers.
ISO 14001:2015
The ISO 14001 environmental management system is a systematic framework to manage the immediate and long-term environmental impacts of an organization’s products, services, and processes. All of our facilities are certified under this requirement. This certification is extremely important to us and we take pride in meeting and exceeding industry expectation like optimizing resource efficiencies, reducing waste, and improving our overall environmental impact. As an environmentally responsible organization, we understand the importance of being a sustainable organization and the prestige that this certification holds.
OEM Supplier Honors
We are a seven-time recipient of the Toyota Distinguished Supplier Award and a four-time winner of the Chrysler Gold Pentastar Award. We are always honored to be recognized for excellent performance in quality and delivery, but these awards mean more to us because of the long partnership we have built with our customers. Chrysler and Toyota have been long term partners for us and receiving honors like this proves that our thermoformed solutions make a true difference in the industry.
Penda’s Quality Testing
The quality tests we perform at Penda are used to gauge and control the quality of the materials we use, and the solutions we provide. All inbound material is tested by our Quality Control department as it arrives at the facility each day. Upon completion and passing, the material is approved for use in production.
Thermal Cycle/Heat Age Test
This test gauges the heat aging of plastics under a simulated solar load. It tests the thermal conditions to which plastics could be exposed to in order to gauge their resistance to oxidation or other types of degradation occurring over time at an elevated solar load. Thermal testing is crucial to our production process because it assures that the plastic we use and the products we produce can stand up to extreme temperatures.
Melt Flow Rate Test
This test is used to determine the rate of extrusion for molten thermoplastic resins using an extrusion plastometer. The melt flow rate test is an important part to the quality checking process as it confirms that the incoming materials we receive are composed of the right resins. If a material undergoes this test and the results aren’t as expected, this confirms that an unknown material is in the sample.
Density Test
By utilizing a benchtop liquid density column, our teams can determine the density of solid plastics with this method. The density test confirms the quality and uniformity of incoming materials after their density is determined.
Coefficient of Friction Test
The Coefficient of Friction (COF) test is a standard practice for determining the coefficients of starting and sliding friction of plastic sheeting. This test is extremely important when producing products like bedliners and pallets. The COF test assures that we produce an end product with a surface that holds the items in your truck bed or on the pallet on your forklift still and steady.
Hot Air Orientation Test
This test allows us to determine the degree of unrestrained linear thermal shrinkage at given temperatures of plastic sheeting using a standard industrial oven. The hot air orientation test pinpoints certain temperatures that incoming materials will experience shrinkage before they are sent to production.
Microwave Furnace Testing
By using a standard industrial ash furnace, the Microwave Furnace Test mesures the ash content of Carbon black. The ash content is typically composed of the water used from manufacturing and a catalyst. Microwave furnace testing lets us know how much of non-carbon components are present in the materials after combustion, so that we know exactly what is in the materials we use.
Surface Resistivity Test
The Surface Resistivity test covers the direct current procedure for the measurement of DC insulation resistance, volume resistance, and surface resistance. It is performed using a surface resistivity meter. Performing this test allows us to ensure the surface resistance of materials used to make products like drop-in bedliners, which need to be skid resistant to keep things from sliding around in the back of a truck bed.
Every company can strive for a commitment to quality but at Penda it is at the forefront of everything we do. We have the customers, certifications, and processes in place to achieve outstanding quality with every product. To learn more about custom thermoforming solutions that you can implement in your business, contact us today and a member of our team will be in touch shortly.